Main properties of plastic raw materials used for enclosures
Electrical and mechanical characteristics of plastics used in immersion heater and temperature sensor housings
Summary of characteristics
Material | PC (Transparent) | 25% Fiber glass reinforced PA66 (Black) | PP (Orange) | PVDF (white) |
Heat deflection temperature under load according to ISO 75
(Values provided by comparative testing made in our laboratory) |
120°C
(1.8 Mpa) |
226°C
(1.8 Mpa) |
64°C
(1.8 Mpa) |
80°C
(1.8 Mpa) |
Impact resistance on 3 mm thickness board, at 25°C, according to EN50102 | IK10** | IK10** | IK10** | IK09 |
Loss of mechanical strength After 1000h UV tests, according to ISO4892-1* | Average: loss of 11% of mechanical strength after 1000h | Excellent : loss of only 7% of mechanical strength after 1000h | 17.53% | 24.78% |
Flammability according to UL94 | UL94-5V | UL94 VO and UL94-5V depending on thickness | UL94VO | UL94VO |
Mechanical strength according to ISO 527-2 | 70 Mpa | 150 Mpa | 26 Mpa | 57 Mpa |
Glow wire flammability index (GWFI), according to IEC 60695-2-12 | 850°C | 960°C | 725°C | 960°C |
Main use in enclosures | Used for clear covers because it offers very good light transmission (85 to 90%), excellent shock resistance, and withstands high ambient temperatures. Its good UV
resistance makes it suitable for outdoor use. Limited resistance to acids, oils and fuels. |
The best compromise between impact resistance, temperature resistance, fire resistance and UV resistance. Usable in most industrial applications, including outdoors exposed to the sun and inclement weather. Its high resistance to deformation under load at high temperatures is recommended for applications in immersion heaters. Sensitive to concentrated acids, good resistance to hydrocarbons. | Economical solution for acid resistance. Fragile at low temperature, sensitive to hydrocarbons, solvents, acetones and oils. Must not be used at ambient temperatures above 50 ° C. | The ultimate solution for applications in the presence of concentrated acids, but low resistance to deformation under load and temperature. Must not be used at ambient temperatures above 70 ° C |
*: UV resistance is improved by the addition of black pigment (carbon black), and this is the main reason for the black colour of most of boxes for outdoor use.
**: IK10 is the maximum class of impact resistance.
Chemical resistance of plastics (indicative list according to data available from different suppliers)
Material | Good resistance to | Non resistant to |
PC (Transparent) | Acetamide, Amyl Acetate, Ethyl Acetate, Methyl Acetate, Acetone, Acetylene, Butyric Acid, Carbolic Acid (Phenol), Chloroacetic Acid, 30-100% Hydrochloric Acid, 50% Chromic Acid, Cresyl Acid, Mono- Chloroacetic Acid, Hydrogen Fluoride from 20 to 100%, Benzo-Sulfonic Acid, Sulfuric Acid (75-100%), Acrylonitrile, Benzoic Aldehyde, Butyl Amine, Amines, Ammonia 10%, Ammonia Liquid, Ammonia Anhydrous, Acetic Anhydride, Aniline, Dimethyl Aniline, Antifreeze, Aqua regia (80% HCl, 20% HNO3), Asphalt, Benzene, Benzol, Bisulfate and Calcium bisulfite, Carbon bisulfide, Butadiene, Butyl acetate, Butylene, Ethyl- Methyl-Ketone, Ketones, Mono-Chlorobenzene, Chloroform, Ethyl Chloride, Ferrous Chloride, Cresols, Copper Cyanide, Cyclohexanone, Diacetyl Alcohol, Dichlorobenzene, Dichloroethane, Diethylamine, Diethyl Ether, Dimethyl Formamide, Furfural, Hexane, Hydrazine, Hydroxide e barium, Lithium Hydroxide, Calcium Hypochlorite, Kerosene, Lacquers, Calcium Hydroxide CaC (OH) 2, Potassium Hydroxide KOH, Sodium Hydroxide NaCOH (50% and 80%), Morpholine, Barium Nitrate, Copper Nitrate , Nitrobenzene, Nitromethane, Perchlorethylene, Butyl phthalate, Pyridine, Barium sulphate, Turpentine, Tetrachlorethylene, Carbon tetrachloride, Toluene (Toluol), Xylene | 20% Acetic Acid, Arsenical Acid, Carbonic Acid, Citric Acid, Cupric Acid, Fluosilicic Acid, Formic Acid, Nitric Acid (5-10%), Phosphoric Acid (> 40%), Salicylic Acid, Stearic Acid, Sulfuric Acid (< 10%), Butyl Alcohol, Isopropyl Alcohol, Barium Chloride, Benzo-Nitrile, Beer, Barium Carbonate, Gasoil, Ferric Chloride, Cider, Detergents, Petrol, Ferric Nitrate, Formaldehyde 100%, Formaldehyde 40%, Glycerin Engine, Sodium Hydroxide (20%), Aviation Fuel (JP3, JP4, JP5), Lubricants, Calcium Nitrate, Pentane, Brine (Saturated NaCl), Lead Sulphate, Calcium Sulphate, Copper Sulphate, Ferrous Sulphate, Sulfate ferric |
20% Fiber glass reinforced PA66 (Black) | Acetaldehyde, Acetamide, Lead Acetate, Ethyl Acetate, Methyl Acetate, Acetone, Methyl Acetone, Acetylene, Carbonic Acid, Citric Acid, Gallic Acid, Maleic Acid, Malic Acid, Oleic Acid, Salicylic Acid, Stearic Acid, Fatty Acids, Acrylonitrile , Amyl Alcohol, Ethyl Alcohol, Isobutyl Alcohol, Benzoic Aldehyde, Aluns Butyl Amine, Ammonia 10%, Ammonia, Anhydrous, Acetic Anhydride, Carbon Anhydride, Aniline, Dimethylaniline, Asphalt, Barium Chloride, Benzene, Beer, Carbon Bisulfide , Calcium bisulfite, Borax (Sodium borate), Butylacetate, Calgon, Barium carbonate, Calcium carbonate, Gas oil, Ethyl-methyl-ketone, Ketones, Chloroform, Benzyl chloride, Calcium chloride, Ethyl chloride, Ferric chloride, Cider, Barium cyanide, Cyclohexane, Detergents, Diacetone alcohol, Dichloroethane, Diethylamine, Lacquer thinner, Carbonated water, Petrol, Ethanol, Ethanolamine , Ether, Butyl Ether, Diethyl Ether, Ethyl Ether, Ethylene Glycol, Ferric Nitrate, Fuels, Formaldehyde 40%, Dimethyl Formamide, Gelatin, Glycerine, Diethylene Glycol, Heptane, Motor Oil, Mineral and Synthetic Hydraulic Oils, Motor Oils ( 1, 2, 3, 5A, 5B, 6), Diesel Oils (20, 30, 40, 50), Mineral and Synthetic Oils, Linseed Oil, Barium Hydroxide, Calcium Hydroxide, Sodium Hydroxide (20% and 50%) %), Sodium Hydroxide (50%), Iodine, Iso-octane, Cane Juice, Grape Juice, Kerosene, Ketchup, Lacquers, Calcium Hydroxide CaC (OH) 2, Sodium Hydroxide NacOH, Lubricants, Molasses, Naphtha , Barium nitrate, Calcium nitrate, Carbon monoxide, Pentane, Petroleum, Trisodium phosphate, Butyl phthalate, Brine (saturated NaCl), Arsenic salts, Silicone, Liquid beet sugar, Barium sulphate, Ferric sulphate, Barium sulphide, Tetrachlorethylene, Toluene, Varnish, White Spirits, Xylene | Acetic Acid, Benzoic Acid, Hydrobromic Acid, Carbolic Acid (Phenol), Chloroacetic Acid, Hydrochloric Acid, Chloric Acid, Chlorosulfonic Acid, Chromic Acid, Cresylic Acid, Cupric Acid, Fluoboric Acid, Monochloroacetic Acid, Hydrogen Fluoric Acid, Fluosilicic Acid, Formic Acid , Hydrofluorosilic acid, Hydrofluorosilic acid, Nitric acid, Perchloric acid, Benzo- sulphonic acid, Sulfuric acid, Sulfuric acid, Butyl alcohol, Isopropyl alcohol, Propyl alcohol, Amines, Antifreeze, Aqua regia (80% HCl, 20% HNO3), Benzol , Bromine, Chlorine, Chlorobenzene (mono), Copper Chloride, Ferrous Chloride, Cresols, Copper Cyanide, Dichlorobenzene, Ethane, Fluorine, Formaldehyde, Calcium Hypochlorite, Sodium Hypochlorite (100%), Sodium Hypochlorite (<20%) ), Copper nitrate, Oleum, Phenol, Calcium sulphate, Copper sulphate, Ferrous sulphate, Carbon tetrachloride, Sulfur trioxide |
PP (Orange) | Acetaldehyde, Acetamide, Lead Acetate, Ethyl Acetate, Acetone, Acetylene, Acetic Acid 20 to 90%, Arsenic Acid, Boric Acid, 20% Hydrogen Bromide, Carbonic Acid, Citric Acid, Cresyl Acid, Cupric Acid, Fluorometric Acid, Hydrogen Fluoride 20% to 50%, Fluosilicic acid, Formic acid, Gallic acid, Glycolic acid, Hydrofluorosilic acid 20% and 100%, Maleic acid, Malic acid, Nitric acid 5 to 20%, Phosphoric acid> 40%, Salicylic acid, Stearic acid , Sulfuric Acid, Sulfuric Acid <75%, Fatty Acids, Acrylonitrile, Rust Removers, Methyl Alcohol 10%, Benzyl Alcohol, Butyl Alcohol, Ethyl Alcohol, Isobutyl Alcohol, Isopropyl Alcohol, Propyl Alcohol, Aluns, Ammonia 10%, Ammonia Liquid, Ammonia, anhydrous, carbonic anhydride (wet), carbon dioxide (dry), aniline, barium chloride, beer, calcium bisulfite, calcium bisulfide, calgon, barium carbonate, carbon carbonate cium, gas oil, chlorobromomethane, calcium chloride, copper chloride, lithium chloride, ferrous chloride, ferric chloride, cider, copper cyanide, detergents, diacetone alcohol, diethylamine, gasoline, ethanol, diethyl ether, ethylene glycol, nitrate Ferric, Fuel oils, Formaldehyde 40%, Dimethylformamide, Gelatin, Glycerin, Diethylene glycol, Motor oil, Aniline, Flaxseed oil, Citric oils, Calcium hydroxide, Sodium hydroxide (20% to 80%), Calcium hypochlorite , Sodium hypochlorite (<20%), Iso-octane, Aviation fuel (JP3, JP4, JP5), Ketchup, Detergent: Calcium hydroxide CaC (OH) 2, Potassium hydroxide KOH, Sodium hydroxide NaCOH, Lubricants, Methylamine , Barium nitrate, Calcium nitrate, Copper nitrate, Lead nitrate, Calcium oxide, Carbon monoxide, Trisodium phosphate, Pyridine, Brine (Saturated NaCl), Silicone, Liquid beet sugar, Lead sulphamate, Calcium sulphate , Copper sulphate> 5%, Sul Iron Ferric Sulfate, Varnish | Methyl Acetate, Chlorosulfonic Acid, 10% Chromic Acid, Chromic Acid, Concentrated Nitric Acid, Benzosulfonic Acid, Benzoic Aldehyde, Maleic Anhydride, Dimethylaniline, Antifreeze, Benzene, Carbon Bisulfide, Carbon Bisulfide, Bromine, Anhydrous Liquid Chlorine, Amyl Chloride, Ethyl Chloride, Cresols, Barium Cyanide, Cyclohexan, Cyclohexanone, Dichloroethane, Lacquer Thinner, Chlorine Water, Ethane, Ethanolamines, Ether, Butyl Ether, Ethyl Ether, Fluorine, Furfural, Mineral and Synthetic Hydraulic Oils, Mineral and Synthetic Hydraulic Oil , Aromatic hydrocarbons, Lacquers, Oleum 25% to 100%, Diphenyl oxide, Pentane, Perchlorethylene, Turpentine, Tetrachlorethylene, Carbon tetrachloride |
PVDF (white) | 20% Acetic Acid, Acetic Acid, Adipic Acid, Arsenical Acid, Benzoic Acid, Boric Acid, 20% and 100% Hydrogen Bromide, Butyric Acid, Carbolic Acid (Phenol), Carbonic Acid, Chloroacetic Acid, 20% to 100% Hydrochloric Acid, 5% to 50% chromic acid, citric acid, Fluorometric acid, 20% to 100% hydrofluoric acid, Fluosilicic acid, Formic acid, Gallic acid, 20 and 100% hydrofluorosilicate acid, Linoleic acid, Maleic acid, Malic acid, Nitric acid (20%) 90%), Oleic Acid, Perchloric Acid, Salicylic Acid, Stearic Acid, Sulfuric Acid, Sulfuric Acid (10 to 100%) | Acetaldehyde, Ethyl Acetate, Acetone, Methyl Acetone, Chlorosulfonic Acid, Methyl Ethyl Ketone, Cyclohexanone, Diacetone Alcohol, Diethylamine, Dimethyl Formamide, Lacquers, Sodium Hydroxide (NaCOH) |
Heat deflection temperature under load according to ISO 75-2
Determination of the temperature of deflexion under load upon ISO75-1 and 3,, is an important parameter to judge of the ability of a plastic raw material to withstand a temperature rise without loosing its mechanical strength. This value is requested by some appliances and commercial standards. As we neeed to compare the various raw materials used in enclosures, all tests have been made in the same condition, under 1.8 MPa load applied at the center of the 10mm width, on 80 x10 x 4mm specimen (Method Af), The 4mm thickness as been selected as being, in the standard choice, the nearest value to the thickness used on plastic enclosures. The temperature rise is 2°C per minute.
The final temperature is registered when the deflexion has reached 0.34mm
Heat deflection temperature under load according to ISO 75, made in our laboratory
![]() |
|
||
Test Equipment | Test specimens | ||
Comparative testing values | |||
PP | PC | PA66 25% FG | PVDF |
63.6°C | 119.6°C | 225.6°C | 80.4 °C |
UV resistance, upon IS04892-1
The main problem of plastic cases is their aging in the presence of UV radiation. Most materials, when exposed to solar radiation, become discoloured and lose their mechanical strength. Therefore, the development of our boxes must take into account this parameter.
The validation tests of the boxes are done by subjecting them to a UV flux, wavelength 315 ~ 400nm, on standardized specimens, at a temperature of 55°C, for 1000 hours, equivalent to several years of sun exposure. These tests are carried out according to standard IS04892-1.
There is no discoloration noticeable on the PA66 cases, and a slight yellowing on the polycarbonate covers.
The loss of Izod mechanical tensile strength is less than 15%, which further complies with UL 746C for enclosures to resist solar exposure.
For information, under the same conditions current boxes in ABS lose 18 to 20% of their resistance.
1000 hours UV resistance testing, made in our laboratory, on plastic specimens
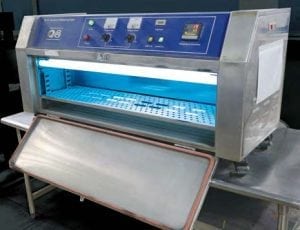
![]() |
![]()
|
![]()
|
|||
Charpy test equipment | Specimen before Charpy impact test | Specimen after Charpy check | |||
Comparative values of loss of mechanical strength (tests made in our laboratory) | |||||
PP | PC | PA66 25% FG | PVDF | ||
17.53% | 12% | 11.7% | 24.78% |
UV colour change measurement (Made in our laboratory)
A comparative examination is carried out between tested and non tested specimens, with measurement of the color change. Color fading is measured with an electronic measurement equipment. Colour change is considered as not visible by a non trained observer when the ΔE is lower than 2.5. This is therefore the reason why we selected a ∆E of 2.5 as the acceptable limit for this test.
For information, a non trained observer can quite easily see the colour difference with a ∆E of 5. A well trained operator can see an average ∆E of 2. The human eyes cannot see a ∆E of 1.
![]() |
![]() |
||
Measuring equipment | Measuring ΔE on an enclosure cover | ||
Comparative values of color fading after UV (tests made in our laboratory) | |||
PP | PC | PA66 25% FG | PVDF |
ΔE: 4.58 | ΔE: 1.29 | ΔE: 3.19 | ΔE: 2.88 |
Resistance to corrosion by chlorine, tests performed in our laboratory according to ASTM G48
The test of resistance to corrosion by chlorine is intended to verify the behavior of plastic housings in a chlorinated medium, such as swimming pool and water recreation premise. Test is performed according to ASTM G48: it consists in a 96 hours accelerated corrosion test at 70°C in a concentrated solution of 5.25% sodium hypochlorite (bleach).
- The loss of mechanical strength is observed by a shock test on a Charpy notched specimen before and after the
- Weight loss is
- A comparative examination is carried out, with measurement of the color As for UV, we selected a ∆E of 2.5 as the acceptable limit for this test.
Chlorine resistance test made in our laboratory
![]() |
![]() |
||||
PC | PA66 | PP | PVDF | ||
Weigth change | +1.06% | +2.34% | +1.47% | 0% | |
Mechanical strenght loss |
-10% | -12.9% | -10.6% | -11% | |
Color change | ΔE: 7.44 | ΔE: 30.67 | ΔE: 13.7 | ΔE: 7.96 |
Flammability checking according to UL94, made in our laboratory
The flammability test of the plastics of the enclosures is intended to verify that the accidental ignition of these will not spread and that the ignition will extinguish itself. The class usually required by certification laboratories is UL94-VO, or for some special cases, the highest class, UL94-5V. All the plastics of the boxes are at least UL94-VO in the thicknesses used.
![]() |
![]() |
![]() |
Testing equipment | Specimen before testing | Specimen during UL94VO checking |
Gaskets used on enclosures, cable glands and fittings
These gaskets are made of elastomer because it is their flexibility and resilience that guarantees the tightness of the closure. The elastomer used as standard is silicone, because of its flexibility, its resistance to UV and common atmospheric pollutants, and its durability. The joints are molded and applied in specially designed grooves.
However, silicone is not universal, especially when it comes to applications in surface treatment baths or in the presence of acids. It is therefore possible to equip most enclosures with FKM (Viton) fluoroelastomer gaskets
Indicative and non-limiting list and products not compatible with silicone seals: Acetone, Hydrobromic Acid, Butyric Acid, Carbolic Acid (Phenol), Hydrochloric Acid, Hydrogen Fluoride, Nitric Acid Phosphoric Acid, Sulfuric Acid, Butyl Alcohol, Benzene, Fuel Diesel, Ethyl methyl ketone, Petrol, Tetrachlorethylene, Carbon tetrachloride, Trichlorethylene, White Spirits, Xylene.
Non-limiting list of products compatible with FKM gaskets: Acetone, Acetic acid, Hydrobromic acid, Acid, Carbolic acid (Phenol), Hydrochloric acid, Chromic acid, Citric acid, Hydrochloric acid Lactic acid, Linoleic acid, Acid Maleic Acid, Oleic Acid, Phosphoric Acid Sulfuric Acid Methyl Alcohol Ethyl, Methyl, Propyl Alcohols; Benzene, Benzol, Chloroform, Calcium Chloride, Detergents, Ether, Ethylene Glycol, Fuel Oil, Hydraulic Oil and Engine Lubricants, Car and Aircraft Fuel, Calcium Hypochlorite, Sodium Hypochlorite, Tetrachlorethylene, Carbon Tetrachloride, Toluene (Toluol), Trichlorethylene, Xylene.
ROHS and Reach
Rohs: the materials used in the boxes comply with the European directive 2015/863 Annex II amending Directive 2011/65.
Certificates made by an accredited external laboratory available on request.
Reach: The materials used in the boxes comply with the REACH European Directives according to the June 2017 directive adding
173 substances SVHC (Substances of Very High Concern) from the list published by ECHA on 12 January 2017, applying to the
directive Reach 1907/2006.
Certificates made by an accredited external laboratory available on request.